There are many different materials helmets can be made out of.
But the two most common shell materials for folding bike helmets are ABS and polycarbonate.
Which one is better?
It depends. On a high level, polycarbonate is more expensive, flexible, softer, and lighter. Conversely, ABS is much cheaper, as well as harder, heavier, and more brittle.
So if you want a helmet that’s thin and light, you’re much more likely to find that in a polycarbonate shell. On the other hand, if you’re looking for a helmet that’s cheap, or offers more scratch resistance, then ABS is the better bet.
But first, let’s begin with an overview of what makes ABS and polycarbonate special. You’ll notice right away that they have a lot in common.
What ABS and Polycarbonate Have in Common
Both ABS and polycarbonate are plastic, like much of the rest of your helmet.
They Are Good Engineering Materials
There are a few physical properties that make both ABS and polycarbonate useful for engineering.
What makes them great for helmets is that they are resilient to impact, and can survive a wide range of temperatures.
This is important, since standard helmet safety tests don’t just measure ability to withstand a crash– they also test the helmet’s performance under extreme conditions (hot, cold, dry, wet, etc).
They Can Take A Hit
If you look at impact strength, or ability to withstand a suddenly applied load, polycarbonate and ABS are both extremely strong.
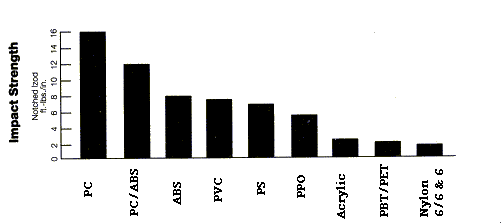
You can see in the image above that polycarbonate has twice the impact strength of ABS. Despite polycarbonate’s extraordinary impact strength, ABS still has a higher impact strength than any of the other common engineering plastics.
Or to put it another way…
Sword VS Polycarbonate Viking Shield
In addition to their high impact strength, both ABS and polycarbonate also have high tensile strength and shock absorbance. These properties make ABS and polycarbonate excellent choices if you want a helmet shell that can take a blow.
They Work When It’s Hot or Cold
ABS and polycarbonate don’t crack under cold temperatures, or burn or melt at high temperatures. The fact that they work in freezing or hot conditions is critical if you want your helmet to get approved by almost any standard helmet safety test.
They Are Easy to Work With
ABS and polycarbonate are amorphous, and very pliable at high temperatures. This makes it super easy to turn them into a helmet shell through either a vacuum forming or injection molding process. The ability to work them into practically any shape makes ABS and polycarbonate attractive materials for a helmet.
You can also color them however you want, or even keep them translucent. ABS is white or translucent ivory and polycarbonate is transparent. This lack of color makes them easy to color, allowing your helmet to be made to look however you want.
Since color, shape, size, and design are key factors in selecting a helmet, the ability to make ABS or polycarbonate take on any form and color makes them ideal materials for a helmet.
They Are Both Thermoplastics
Thermoplastics are easy to mold at high temperatures. Having a thermoplastic shell means that the shell can be made in the same mold as the rest of the helmet, rather than being glued on after the fact like some lower end helmets.
This is why being made in a single mold matters:
You Can Make a Thinner Helmet
First off, it allows the helmet to be thinner and airier, since the helmet holds together better in an impact.
However, a consequence of being thin and airy is that an impact can become localized. This means that the force gets focused on one area. That can be dangerous for people with more fragile heads.
You Can Recycle It
The second benefit of thermoplastics is that they can, theoretically, be recycled. Although note that in practice it’s not so easy to recycle your helmet. Your helmet shell may, however, be made from recycled material.
ABS
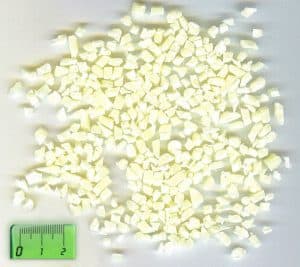
Acrylonitrile Butadiene Styrene, or ABS, is a widely used plastic with many desirable properties. In fact, it combines the best properties of acrylonitrile, butadiene, and styrene to make a plastic that is one of the most versatile in the world– you see it on pipes, computer keyboards, luggage cases, wall socket covers, LEGOs, clarinets, and on and on. It’s also a very popular 3D printing material. And of course, you’ll find it on helmets.
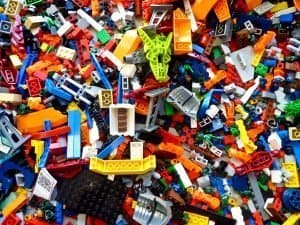
How ABS Got to Be so Strong
The discovery of ABS began in the 1930s with polystyrene, a clear, hard, brittle, plastic that’s prone to melting if it gets hot. In the 1940s, acrylonitrile was added to the mix, leading to styrene-acrylonitrile, a polymer that was still clear like polystyrene but didn’t break or melt as easily. Finally, in 1948, chemists started adding polybutadiene, a synthetic rubber that’s flexible, pliable, and resistant to wear. The combination of those three chemicals produced Acrylonitrile Butadiene Styrene– ABS.
The Amazingness of ABS
ABS had the best qualities of each of its components. Like polystyrene, it was hard and colorless. The acrylonitrile made it resistant to breaking and melting. And the polybutadiene made ABS pliable yet tough, and strong even at low temperatures.
On top of all that, ABS can be easily recycled by melting and cooling. It can even be recycled over and over again without any degradation of its amazing properties. This means that ABS is not as damaging to the environment as its more disposable plastic cousins, and its energy and fossil fuel consumption is relatively limited.
And being that it’s made out of relatively cheap synthetic products, ABS is extremely affordable. It can even be as cheap as $1.50/lb.
ABS Qualities
Here are some of the useful qualities of ABS:
- Extremely strong and rigid (from the styrene-acrylonitrile)
- Shiny, scratch-resistant surface (from the styrene)
- Stable at high temperatures (from the acrylonitrile)
- Resilient, with high impact resistance (from the butadiene rubber)
- Tough even at low temperatures (from the butadiene rubber)
- Partially resistant to chemicals and weathering (from the butadiene rubber)
- Safe (not carcinogenic)
- Colorless
- Can be processed easily (machined, cut, drilled, etc)
- Can be melted down and recycled
- Very cheap
But it does have its downsides, too:
- Direct sunlight causes it to degrade and turn yellow over time
- It’s heavy, compared to polycarbonate
- It’s not nearly as strong as polycarbonate
These downsides bring us to our next awesome helmet shell thermoplastic.
Polycarbonate

Polycarbonate (PC) is the product of two rather unappealing chemicals: BPA and a gas used primarily as a chemical weapon in WWI. When combined, however, the result is not only safe, but is actually used to save lives.
Polycarbonate is extremely strong– it has a much higher impact strength than the next strongest common engineering plastic, ABS. This makes polycarbonate a key ingredient in the manufacture of bulletproof glass. Layering a sheet of polycarbonate behind a sheet of glass allows the bulletproof glass to only partially shatter while still absorbing the energy of the bullet.
Since polycarbonate is so strong– yet transparent– it has become a hugely popular material for a variety of products. It is used for phone cases, bottles, riot shields, high-temperature Tupperware containers, luggage, windshields, DVDs, contact lenses, medical devices, and so on. Of course, it is also used as a shell material for helmets.
What Makes Polycarbonate Special
The combination of super high impact resistance and tensile strength, paired with polycarbonate’s transparency, is what makes it so useful. For most structural properties, polycarbonate performs much better than ABS.
You would think there would be some tradeoffs here. But surprisingly, there aren’t a whole lot, aside from its price. Polycarbonate can cost several times more than ABS does, but if you’re willing to shell out for it, you will get a superior product.
Polycarbonate Qualities
The list of polycarbonate’s ridiculously convenient features seems almost endless.
- Extremely strong and flexible (even more so than ABS)
- Flexible, with very high tensile strength (twice that of ABS)
- Stable at high temperatures (works at much higher temperature than ABS– 130 ºC vs 80 ºC)
- Resilient, with high impact resistance (more than ABS)
- Tough even at low temperatures (works at much lower temperature than ABS– -40 ºC vs -20 ºC)
- Resistant to chemicals and weathering (resistant to UV light, whereas ABS would degrade)
- Safe (exclusively used by medical devices)
- Transparent (can make more colors and patterns than ABS)
- Can be processed easily (machined, cut, drilled, etc)
- Can be melted down and recycled
- Self-extinguishing (will cease burning once you remove the source of the flame)
You can see from the list above that in almost any feature you look at, polycarbonate is at least as good as ABS, and is typically better.
The only downsides? Polycarbonate is:
- More expensive than ABS
- Not scratch resistant
Side-By-Side Comparison of ABS versus Polycarbonate
Let’s look at that list again, this time comparing ABS to polycarbonate side-by-side.
ABS | Polycarbonate | |
Price | About $1.50 / lb | About $3.00 / lb |
Workability (ease of machining, drilling, cutting, etc) | Easy | Easy |
Recycleability | Easy, at certain facilities | Easy, at certain facilities |
Flexibility | Rigid | Flexible |
Impact Resistance | High | Extremely High |
Heat Resistance | Works up to 80 ºC | Works up to 130 ºC |
Cold Resistance | Works down to -20 ºC | Works down to -40 ºC |
Chemical Resistance | Good | Good |
UV Resistance | Bad | Fair |
Fire Resistance | Ignites at 416 ºC | Ignites at 580 ºC. Self-extinguishing |
Safety | Non-toxic, but not suitable for medical implants | Non-toxic, used exclusively in medical implants. But may release BPA |
Color | Translucent, white | Transparent |
Surface Texture | Shiny, resists scratches | Can get scratched |
You can see from the list above that ABS is a pretty good material, but not as good as polycarbonate.
The main drawback of ABS is that it degrades in UV light.
Conversely, the main drawback of polycarbonate is its high price and that it can get scratched.
ABS vs Polycarbonate for Folding Helmets
Overall, polycarbonate is generally considered a higher end helmet material, due to its having a high impact resistance for its weight. Because of this property, polycarbonate helmets are often thinner and lighter, while offering the same level of protection as ABS helmets.
Nevertheless, ABS helmets do have an aesthetic advantage over polycarbonate helmets in that their surface does not scratch as easily.
Polycarbonate shell helmets tend to be more expensive than ABS helmets.
ABS | Polycarbonate | |
Price | Low | High |
Hardness (Scratch Resistance) | High | Low |
Weight | High | Low |
Impact Resistance | Low | High |
Bottom Line: Should I Buy a Helmet Made of ABS or Polycarbonate?
In general, helmets made of ABS are cheaper and heavier, but don’t scratch as easily. Polycarbonate helmets tend to be thinner and lighter, but also more expensive and will scratch more easily.
The main questions you should ask are:
- Is the helmet in my budget? Polycarbonate shell helmets tend to be more expensive than helmets with ABS shells. Get the helmet that you can afford and will wear.
- Does the helmet look and feel good? Higher end helmets tend to look and feel better than lower end helmets. They will also tend to be made with polycarbonate shells. So if you like the helmet in general, you should buy it. You’ll be more likely to wear a helmet that you like, which is the most important consideration.
- Is the helmet thick enough to protect my head? Helmets made from polycarbonate may be thinner and lighter than helmets made from ABS. Although they are presumably both safety certified in the country where you live, the thinner helmets will tend to localize the impact. This can matter for people who have a more fragile head, such as seniors. If that’s the case, you may prefer a thicker helmet, even if it’s made out of the heavier ABS.
- Will I be wearing the helmet for very long rides? If you plan on having long bike rides, an ABS shell helmet will tend to be heavier and therefore less comfortable over the long haul. So if you love long biking trips, consider getting a helmet with a polycarbonate shell.
- Do I care if the helmet gets scratched up? Small surface scratches should not affect the safety of the helmet, since most of the impact is absorbed by the EPS liner. However, there is definitely an aesthetic element to having a shiny, flawless helmet exterior. If this is something you value, then consider getting a helmet with an ABS shell.
How Do I Know What the Helmet Shell Is Made Of?
Look at the technical specifications for the helmet you are considering buying. They will typically give the material of the helmet. The specs will often specify both the lining material as well as the shell material.
They will typically look something like this:
Lining Material: EPS
Shell Material: PC
If you see PC, then you know the helmet shell is made of polycarbonate.
Who Needs a Shell, Anyway?
Until recently, all of the folding helmet shells have been made of either ABS or polycarbonate. That’s because the inside of helmets, or the liner, is typically made of a relatively fragile material called Expanded Polystyrene (EPS) which needs to be held together by a harder plastic to keep it from quickly degrading.
But recently, two folding helmets have entered the market that are not based in EPS and therefore do not need a hard plastic shell at all.
- Hedkayse is a folding helmet made out of a proprietary material called Enkayse. The tough foam-like material can take impact after impact without noticeable damage, unlike most helmets. So while most helmets have to be thrown out after a single impact, Hedkayse can take a hit over and over again without having to be replaced.
- Cyclo is a folding helmet made out of recycled high-density polyethylene (HDPE). The helmet uses a honeycomb lattice structure to take the impact, rather than an EPS layer. Since it does not use the brittle EPS, it also does not require a shell, and also can also take multiple impacts without having to be replaced.
So if you don’t want a shell at all, look for a helmet that does not have an EPS liner. It may also have the added benefit of not needing to be replaced after a single impact– but check with the manufacturer to be sure.
What Else Should I Look for in a Folding Helmet
Aside from the shell material, you should also think about what kind of buckle your helmet has. Traditionally, most helmets have used side-release buckles. But recently, helmets have started to incorporate newer technology such as magnetic buckles. Read our overview of helmet buckles to learn more.
Check out These Folding Helmets
If you’d like to see more helmets, you can look at our list of folding helmet reviews. These helmets are designed for commuters and people living in cities who don’t have space in their briefcases, offices, or homes for a bulky helmet. Many new folding helmets have hit the market recently, so there’s a lot of competition in this space, and a lot of thought has gone into making them super convenient.
Our website uses affiliate links, meaning that if you click on a hyperlink, we may receive a commission for referring you to the seller’s website. As Amazon Associates, we earn from qualifying purchases. Any prices and availability shown are based on time of publication and may subsequently change.
Helmet Indian standard
Polycarbonate for sure. Though it’s more expense, it’s also more durable, so the quality-price ratio is fairly positive. We’ve been using similar helmets at Agro and we are very happy with them.
basically, polycarbonate protects itself, while ABS protects what’s behind it.
Thumpa up! Detailed article.
I always used to read post in news papers but now as I am a user of web therefore from now I am using net for articles or reviews, thanks to web. <a href=”https://www.updateland.com/”>UpdateLand</a>